At a recent webinar convened on behalf of the Quality Management System Special Interest Group, myself and Q colleagues explored how an NHS organisation could design a quality management system (QMS) to manage the quality of its outputs.
Quality Management System: the basic requirements
I put forth that a QMS begins with designing a product or service realisation system that meets your customer’s requirements. The next step is to manage the processes that form your product or service realisation system. This allows you to ensure that work activities are compliant and the quality of your outputs is assured.
For an organisation to claim that it has a QMS in place, it needs to have systematically documented and recorded results within a specific time frame that demonstrate how the product or service realisation system meets the customer’s requirements.
It must also show that the work activities are compliant to the requirements of this system. The records must include any examples of non-conformance and be able to show, via an audit trail, any corrective and preventative action taken.
Organisations must also document their structure, and provide information on key responsibilities and organisational policies.
Design and process: the keys to a successful QMS
The success of your QMS is down to how you manage the design and process of your organisation. To do this methodically is not a simple task. Quality management is not a new activity and over the years ISO9001 has evolved to become a widely used standard for a QMS in the UK and Internationally.
An organisation’s compliance to ISO9001 can be a ‘work in progress’ project, and an organisation may take some number of years to achieve full compliance.
QMS language and the NHS
During the webinar, a number of participants pointed to the variation in how language is used in the NHS as compared to QMS, and the challenges that this presented.
Quality management is a mature profession. The Chartered Quality Institute has existed for over 100 years in the UK and quality management terminology is very well defined. If they are to demonstrate quality assurance to their stakeholders, most of whom are not employees of the NHS, the NHS could consider adopting existing QMS terminology. In my view, discussion about language should not dominate or delay progress towards quality management in the NHS.
Understanding the building blocks of QMS
In the literature of QMS, W. Edwards Deming is well known for the development of the Plan Do Study Act (PDSA) cycle and his work on product or service design and realisation processes. The work of Deming and Joseph M. Juran form the basic building blocks around which standards for quality management systems have evolved.
Within Deming’s body of work, my favourite is the Red Bead experiment.
The video clips are worth watching.
Juran further developed the PDSA cycle and it became known as the Plan Do Check Act (PDCA) cycle and is the most widely used version in quality management. My favourite is his Trilogy, Quality Planning, Quality Control and Quality Improvement. Please note that in this context, the term ‘quality improvement’ has a different meaning to NHS quality improvement. I’ve produced some notes on this.
How does NHS quality improvement fit into a QMS?
With reference to my notes on Juran’s Trilogy, we need to consider Juran’s two types of beneficial change.
The first relates to changes to the product/service offered or the design of their realisation system. This compares most to what the NHS call QI.
The second relates to improvements to processes within the product or service realisation system to reduce non-conformance and error and increase effectiveness and efficiency.
It is important to differentiate between these two types of change, as they require different techniques and should be undertaken by different work teams. It is also important to note that quality management is a technical activity.
How can QMS be implemented in an NHS Trust?
The requirements (clauses) of an ISO9001 can be approached from both the top and bottom.
The clauses highlighted in red are more relevant to the top team and those in blue to front line staff. Help will be required from an experienced quality professional in undertaking this activity. Establishing a design team and a quality management team may be a necessary starting point. Information technology, patient safety and maybe audit departments will already exist. Not included in the webinar index diagram is finance, which should be included as part of the project.
A starting baseline should be established using some recognised maturity matrix tools and progress measured periodically.
How QMS can reduce errors?
For me this is one of the key outcomes from implementing a QMS. First ‘error’ or non-conformance needs to be defined for the NHS. A process management system, designed to be part of a QMS, will address the problem of error.
Process management has two key aims, first to reduce the number of steps in a process (simplify), and second to eliminate error or non-conformance in its application (error proofing). The process management system can be designed as a learning system as illustrated below.
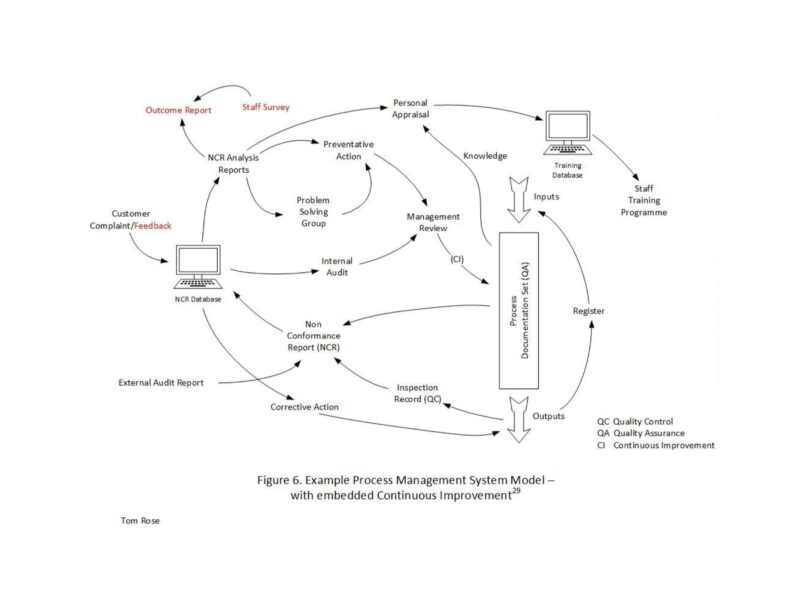
Find out more about QMS
For those who are interested, I invite you to watch our webinar on the Q community Youtube channel.
You can also join our Quality Management in Healthcare Special Interest Group to find out more about upcoming events and ongoing discussions about QMS with other health and care professionals.
And be sure to keep an eye out for my upcoming blogs, exploring Juran’s trilogy and its potential for application in the NHS.
Comments
Michael Ashton 1 Jul 2023
I am a retired Engineer and Lead Auditor.
On a personal level I found this article off-putting to the subject.
Simply put:
QM is not an add on and must be intrinsic to everything we do.
Quality = Conformance to requirements
Quality deliverables i.e. any defined documentation/or evidence designed to confirm to an external entity (if necessary) that we have undertaken a given task in a compliant manner.
These Quality deliverables provide the means by which we are able to Assure. I.e. they provide evidence of conformance to requirements.
QM must be designed to achieve a task with Zero Defects. Getting if right first time.
It is not sufficient in todays complex world to deliver a product. We must deliver an Assured Product.
Audit although used widely is a very blunt tool usually. Reactive rather than pro-active in nature and of limited value if any (in my view)
A basic comprehension of the foregoing is an essential to achieving the creation of effective QM in any area of activity.
Mike Ashton
Thomas John Rose 3 Jul 2023
Mike,
Thanks for your comment. I'm also a retired Engineer (Chartered) and Lead Auditor (including TickIT), also a Chartered Quality Professional with over 40 years of experience. I'm sorry that you found my article off-putting. I'm not sure that you have any knowledge of the situation regarding quality management in the NHS. I understand the situation and I also understand quality management. It would be good if you could add some comments specific to the NHS. Hope to hear from you again.
Regards
Tom